Hello, everyone. Welcome to wearware, your go-to site for shaping the future of the fashion and apparel industry.
The use of 3D objects and virtual samples is becoming increasingly important in fashion, and enhancing their realism depends heavily on material data. With many different types of texture maps such as alpha map, base color map and roughness map, learning and using them may seem intimidating at first. Might we suggest the "U3M" data format that compiles all this 3D information?
This time we introduce U3M as essential knowledge for producing digital fashion by permitting more realistic and convincing product images and presentation materials. Be sure to read on until the end!
From the U3M - Unified 3D Material
Table of Contents
What is U3M?
U3M (Unified 3D Material) is a 3D material data format jointly developed by Browzwear and Vizoo. Materials are crucial elements that control the appearance and texture of 3D objects, requiring detailed settings to achieve more realistic results. U3M files contain two types of information: optical properties*¹ and physical properties*², which make material settings easier to handle.
When U3M files are loaded into 3D software, material information such as the bumpiness, glossiness, and softness of the fabric used in the 3D space is set, allowing you to replicate the texture of the actual fabric. It is indispensable for creating realistic virtual samples.
*1: The properties that describe how an object reflects, refracts, or absorbs light.
*2: The properties that describe thickness, elasticity, bendability etc. of an object.
Benefits of U3M
Easy Data Management
Optical and physical property data are usually generated as separate files. Even when using a single type of material to create 3D virtual samples, you need to handle two different files. If these files are not managed correctly, there's a risk of combining the optical property file with the wrong physical property file, leading to human error. This could result in an inaccurate sample image that differs significantly from the actual product.
In contrast, U3M files, which contain both optical and physical property information, can help avoid such errors. Additionally, 3D material data is often shared between suppliers/vendors and designers during virtual sampling. Using the U3M format makes this process easier and more efficient.
Supplement: U3M consists of a u3m file, a json file (physical property data), and a textures folder (optical property data) stored together in a single folder. When you load a U3M file into 3D software, the linked files are referenced accordingly.
Note: The file structure, other than the U3M file itself, may vary depending on the software used to output U3M.
Data Versatility
U3M is an open format. Therefore, it is supported not only by Browzwear's Vstitcher and Lotta but also by various 3D software like Optitex, APEXFiz® (Shima Seiki), and z-weave (z-emotion). Traditionally, each software used its proprietary file format for material data, but U3M allows data to be used without being tied to a specific software.
From the U3M - Unified 3D Material
How to Create U3M
So, how is U3M created? Broadly speaking, there are two methods: creating it from physical fabrics and creating it virtually.
Scanning Physical Fabrics
Using Vizoo’s xTex Scanner
The most common method involves using Vizoo’s xTex scanner. By scanning the physical fabric, optical property data is created. This data is then enhanced with physical properties measured by Browzwear’s Fabric Analyzer. This method utilizes the equipment from Vizoo and Browzwear, the developers of the U3M format.
From the Vizoo — Polytropon
From the Fabric Analyzer - Compre agora na Software.com.br
Using the Nunox Fabric Scanner
Another company developed a fabric scanner called NunoX, which scans the physical fabric to obtain optical property data and then uses AI to generate the fabric’s physical properties, creating a U3M file. Unlike laborious methods that require a device like the Fabric Analyzer, which necessitates manual measurement of physical properties by an operator, the use of AI makes the file creation process more efficient.
From the NunoX Official site
Using Textura or TextileCloud
Additionally, SEDDI’s Textura and Frontier.cool’s TextileCloud allow you to scan physical fabrics using a common office scanner. AI technology then generates both optical and physical properties, exporting them as U3M files. This method does not require the purchase of special equipment, making it a cost-effective new approach.
From the AI Fabric Digitization - Frontier.cool
Virtual Method Using APEXFiz®
The methods introduced so far for creating U3M files rely on having physical fabric samples on hand. However, it can sometimes be challenging to obtain accurate data due to the condition of the fabric, or you might not have easy access to the physical fabric at all. In contrast, with Shima Seiki's APEXFiz® software, you can create fabrics from scratch on your computer screen and generate U3M files for them.
Note: Since U3M files created with APEXFiz® only contain optical properties, it is recommended to use AI technology from SEDDI’s Textura or Frontier.cool’s TextileCloud to add physical properties.
Please view with the subtitle function turned on.
Creating material data for new fabric designs using scanning methods requires first ordering the fabric and weaving it in a factory, which involves a lead time of 2-3 weeks. Additionally, the primary goal of 3D virtual samples is to minimize the number of physical samples, but weaving fabric for scanning purposes leads to resource waste.
In contrast, the method using APEXFiz® is a 100% virtual solution, eliminating lead time and environmental impact, making it a new sustainable solution.
For detailed information about creating virtual fabrics using APEXFiz®, please see the article below.
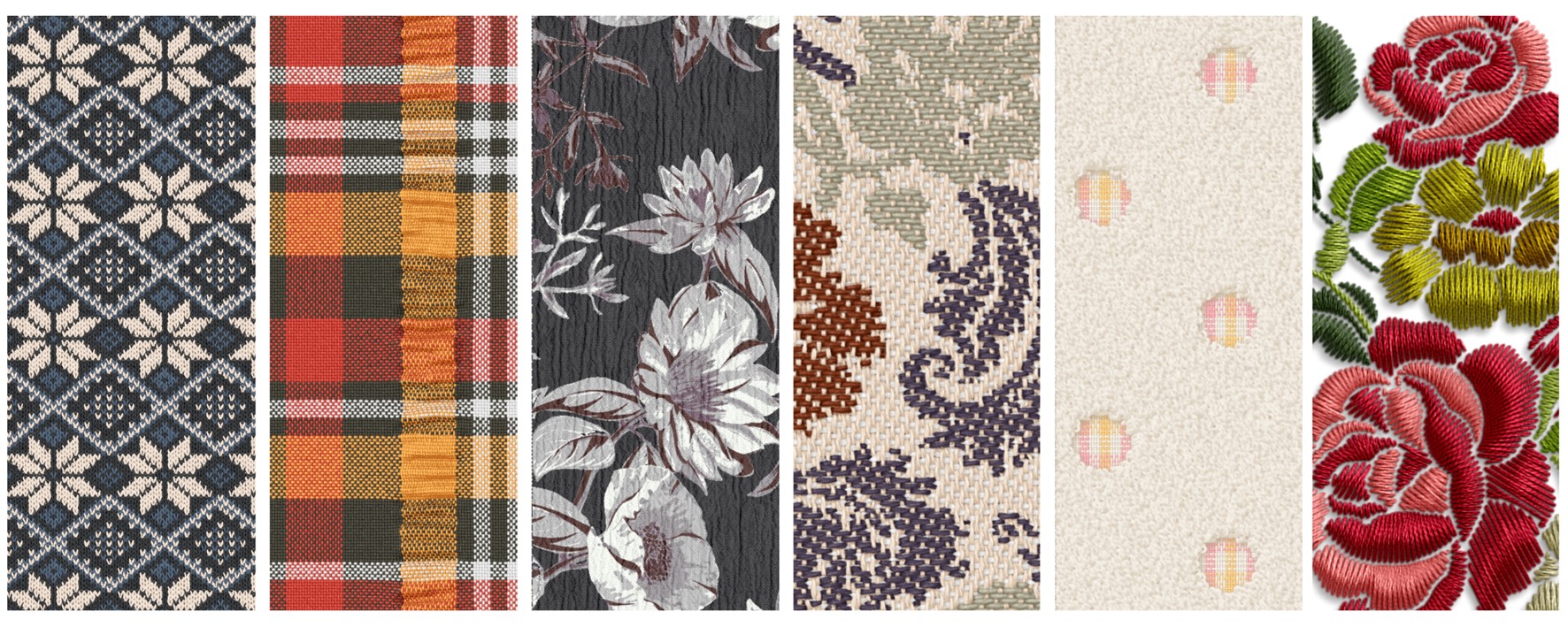
Accelerating DX in Your Planning Work with Fabric Simulation!
In this, our fifth installment in our on-going six-part series on solutions to promote digitalization in the fashion industry, we examine how to create fabrics for weaving, circular knitting, towels, and embroidery. We'll explain how to design and simulate fabrics using design software.
Related Article
How to Share U3M Data
As mentioned earlier, U3M makes it easy to manage texture and shape data related to 3D modeling, and by uploading the data to the cloud, it can be easily shared between suppliers and designers.
For cloud sharing, you can use general services like OneDrive or Google Drive, as well as digital fabric-specific platforms like swatchbook. These dedicated platforms are optimized for sharing digital fabrics, providing features like 3D preview and material information display, making file sharing smarter and more convenient. Besides sharing data with existing partners, these platforms also offer marketplace services where fabric data can be searched, facilitating new business opportunities.
In addition to swatchbook, platforms that support U3M include DMIx. The previously mentioned Textura and TextileCloud also provide platforms that support the U3M format.
Make the Most of U3M!
We hope this session was useful. As you see, U3M is indispensable for realistic 3D virtual sampling, and the methods for generating this file, the 3D software that supports it, and the dedicated platforms for sharing files are expected to continue increasing. By deepening your understanding of the files and their purpose, you can improve your virtual sampling process with higher quality and efficiency.
wearware supports the digitalization of fashion design.
Stay tuned for more updates!